Condition Based Monitoring
Dairy Industry
Requirement
- Condition monitoring of all the compressors
- Monitoring key parameters of individual compressors to optimize maintenance schedules.
- Accurate measurement of each compressor's running hours and discrete energy consumption.
- Monitoring voltage, current, power, speed, and torque of compressors.
- Automated alerts for maintenance needs and process deviations.
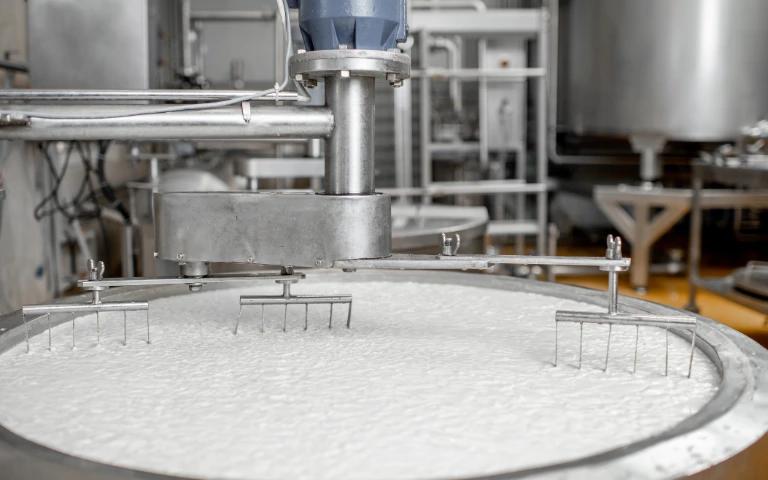
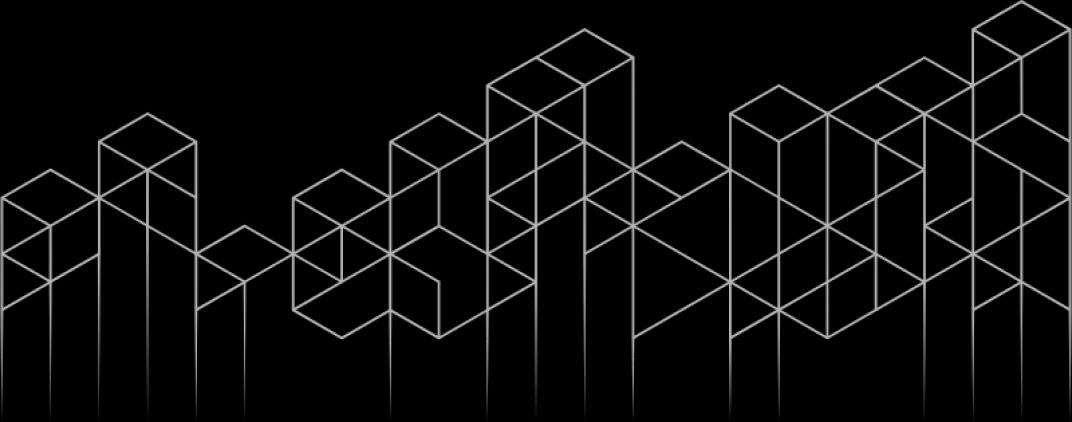
Key Highlights
Enture IIoT implemented a continuous monitoring platform for compressor condition monitoring. The data and insights enabled the maintenance team to adopt predictive maintenance, reducing maintenance costs and extending compressor lifespan
0%
Reduced downtime
extended equipment lifespan
0%
reduction in energy costs
optimizing compressor usage.
0%
reduction in overall operational cost
reduced maintenance costs.
Increased visibility in Factory operation and insights for energy efficiency
Before
- Critical parameters were monitored and recorded manually.
- Compressor maintenance was done in a periodic manner and not as per the machine condition.
- Report generations were done manually and were time-consuming.
- Critical parameter alerts and notifications weren’t present.
After
- Critical parameters were continuously monitored and recorded automatically.
- Discrete energy consumption tracking led to reduction in energy costs by optimizing compressor usage.
- System was configured to automatically trigger notifications and alerts based on predefined conditions.
- MIS reports were configured as per compliance monitoring requirements.
- Timestamped historical data was maintained for long-term analysis, decision making, and audit compliance.