Energy Monitoring
Textile Industry
Requirement
- Continuous energy monitoring for operational efficiency.
- Power Quality Monitoring at incomer for improved equipment life and energy savings.
- Alerts and notifications for critical parameters.
- Visualizations for real-time machine status.
- Analytical tools for data processing based on shifts, machines, process, and department.
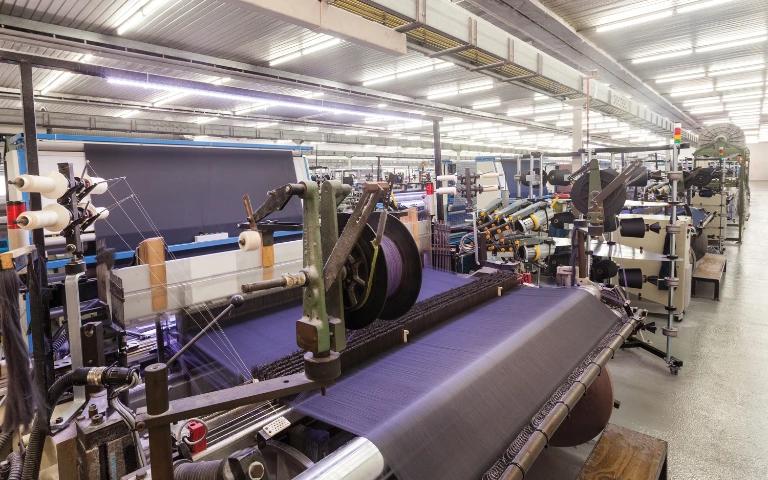
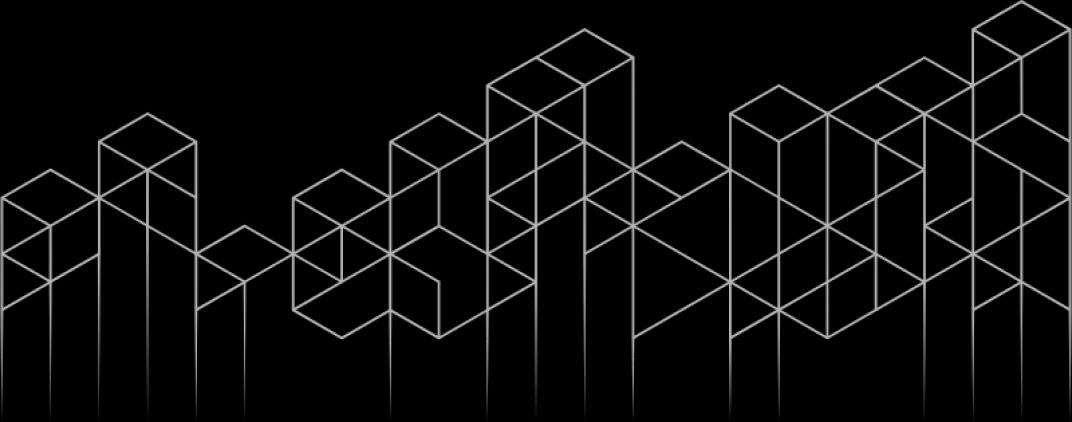
Key Highlights
Enture provided a comprehensive diagnostic tool to the promoter of MSME to take data driven decision for operational excellence and reduce energy consumption
0kWh
Benchmarking and analysis helped
Saving Energy consumption per month
0.Rs
Energy cost savings
Yearly basis
0+
Devices Connected
Across various sites
Increased visibility in Factory operation and insights for energy efficiency
Before
- Manual data recording and analysis with data capturing frequency once in a day.
- Data for individual equipment, section, department was not available.
- Delay in reports and data sharing.
- Limited analytics over the recorded data due to sparse data.
- Average daily energy consumption for lighting was 750 kWh.
After
- Continuous energy monitoring.
- Monitoring and analytics for individual equipment.
- High granular data for detailed analysis on shift, section, and department basis.
- Data and insights enabled management to take corrective action for efficiency.
- Average daily energy consumption for lighting is 660 kWh.